LEAN MFG
LEAN MANUFACTURING
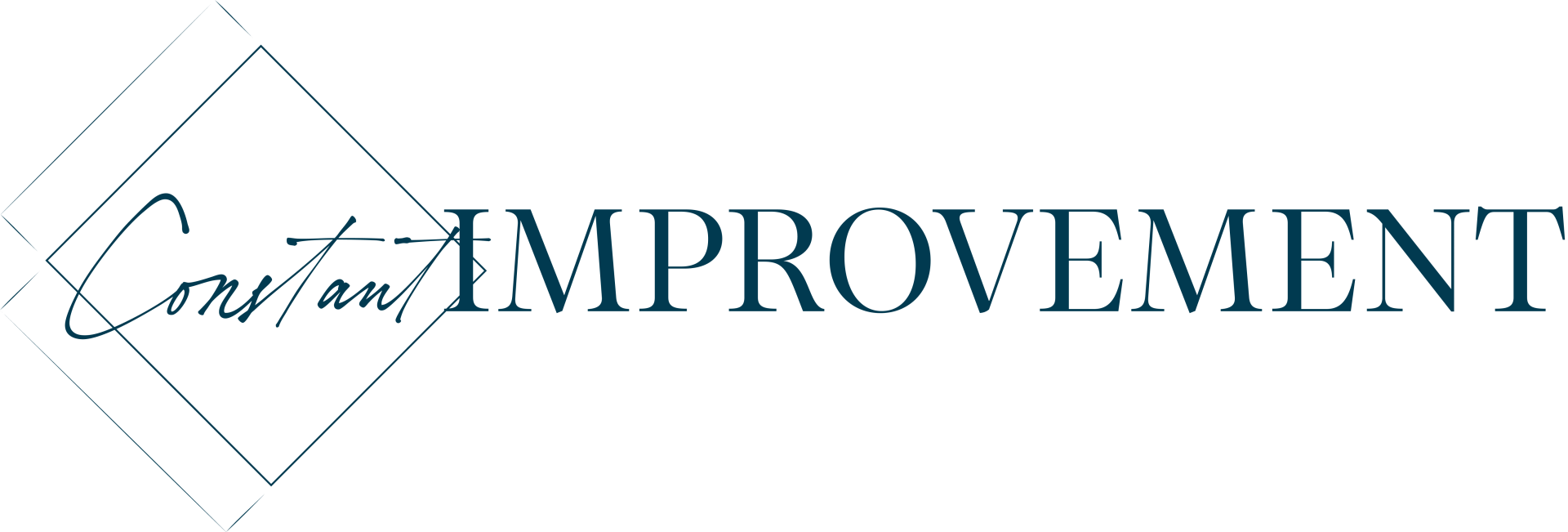

“Something is wrong if workers do not look around each day, find things that are tedious or boring, and then rewrite the procedures. Even last month’s manual should be out of date.”

– Taiichi Ohno
Founder of Toyota Production Systems

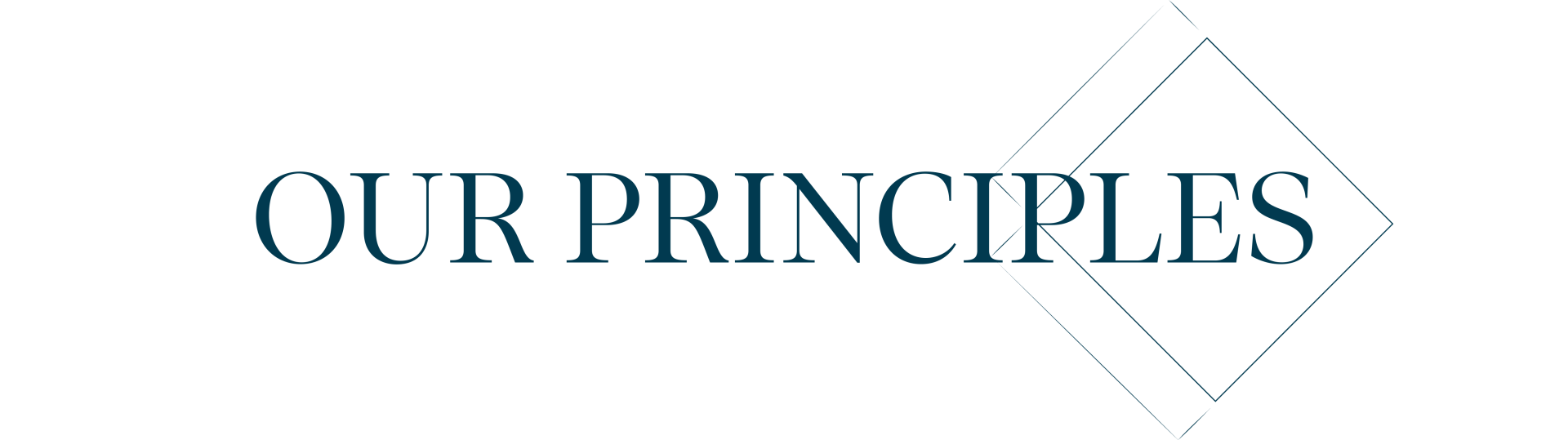
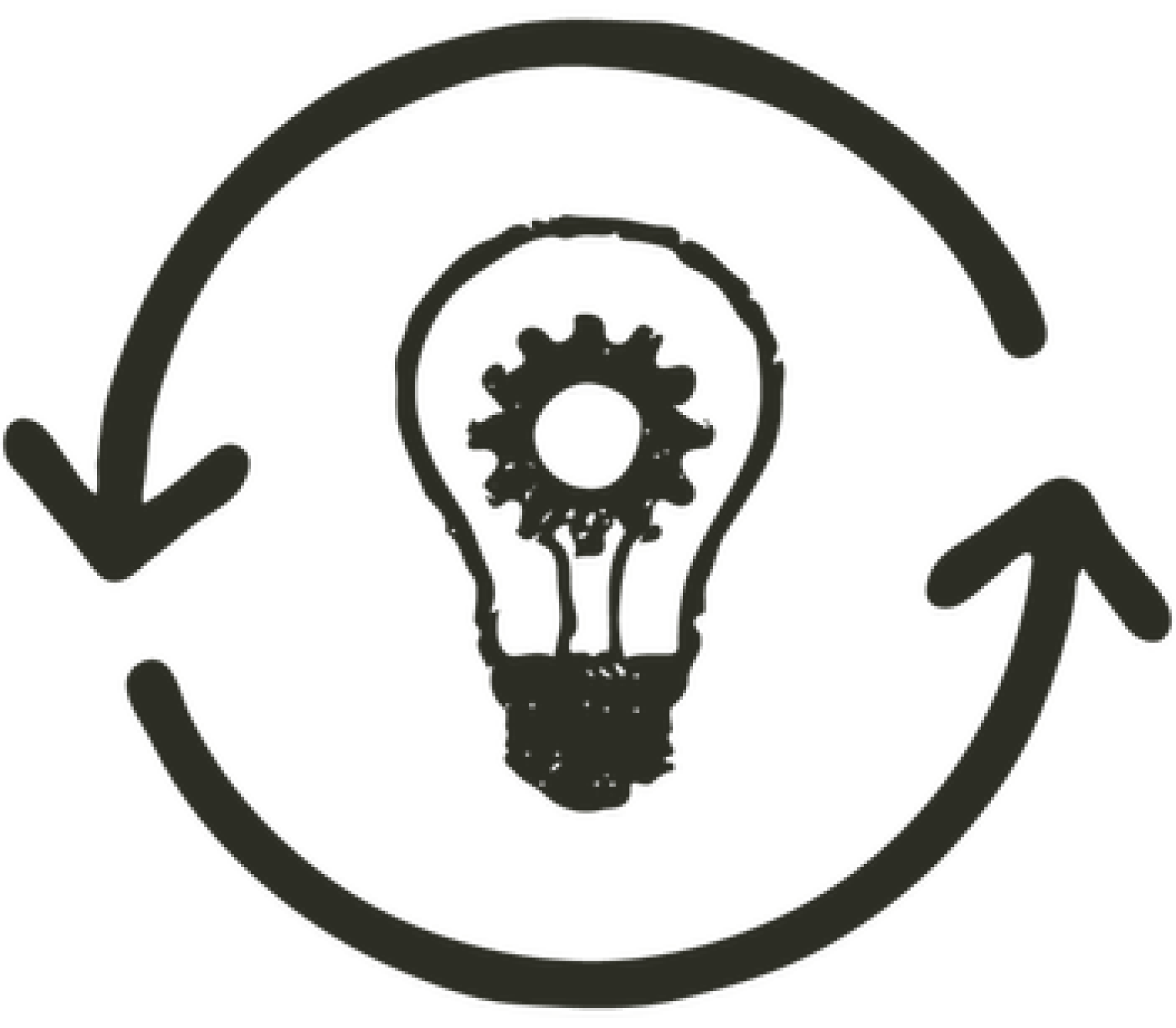

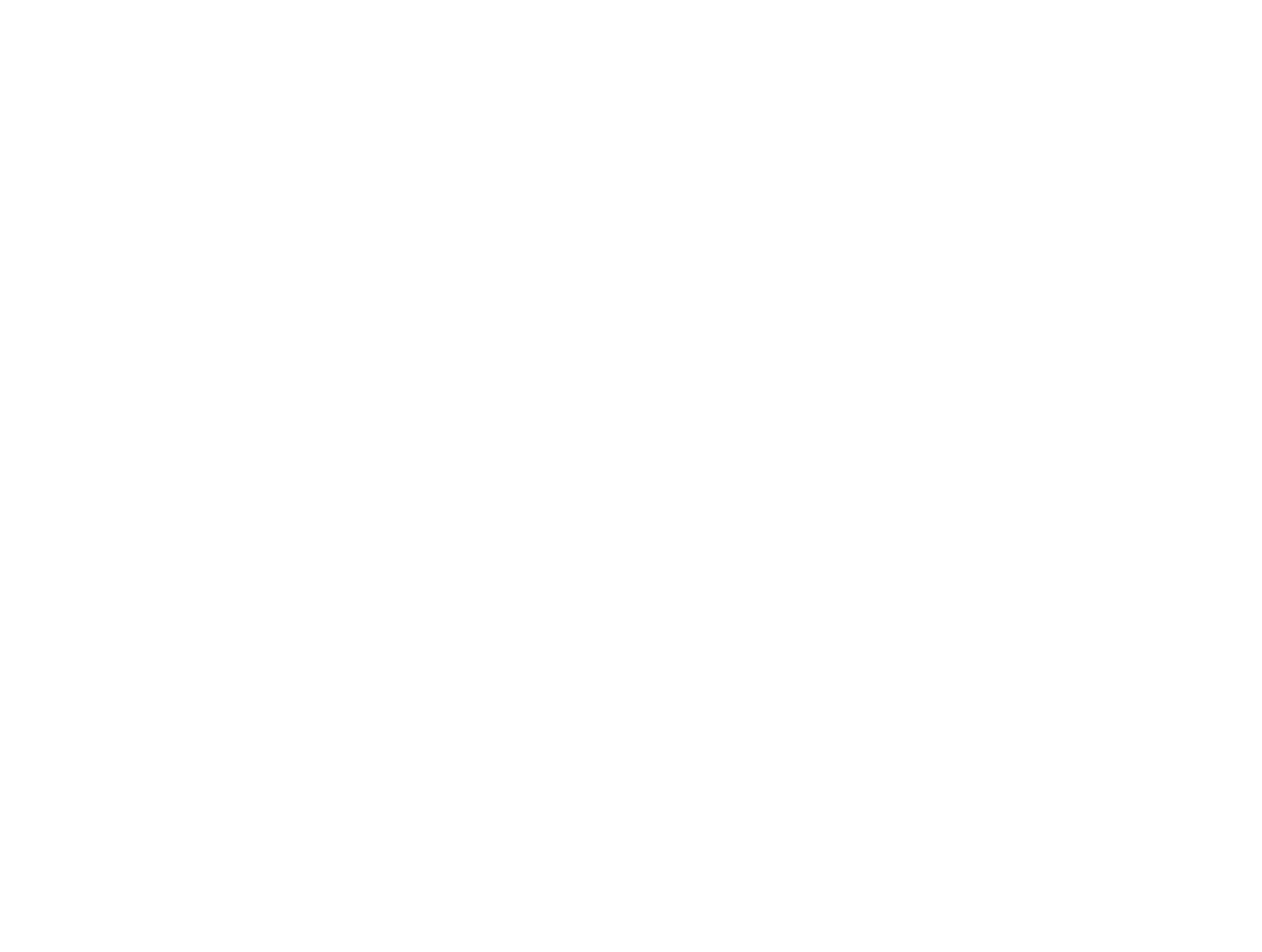
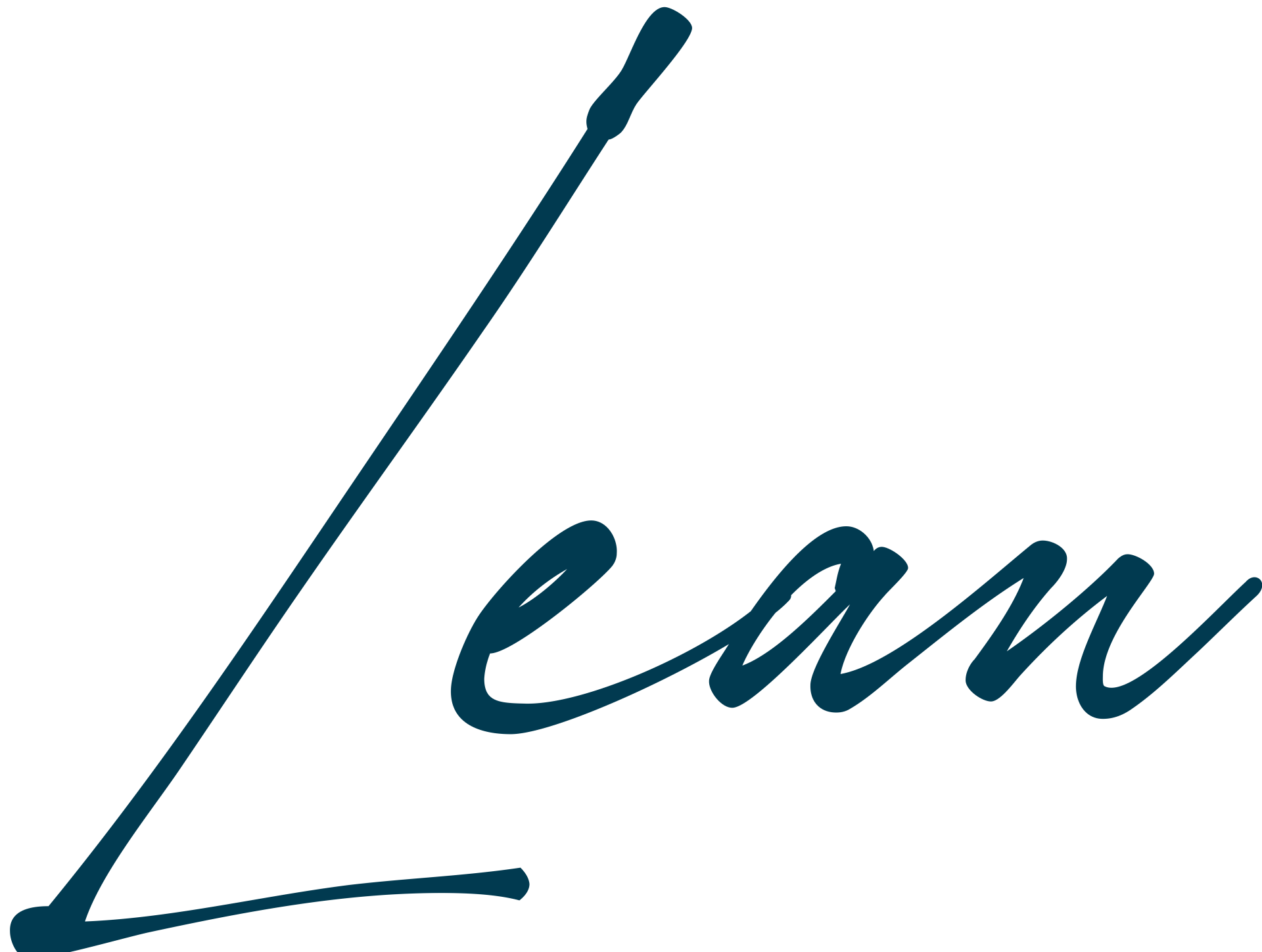
Focuses on efficiency through the minimization of waste errors and delays.
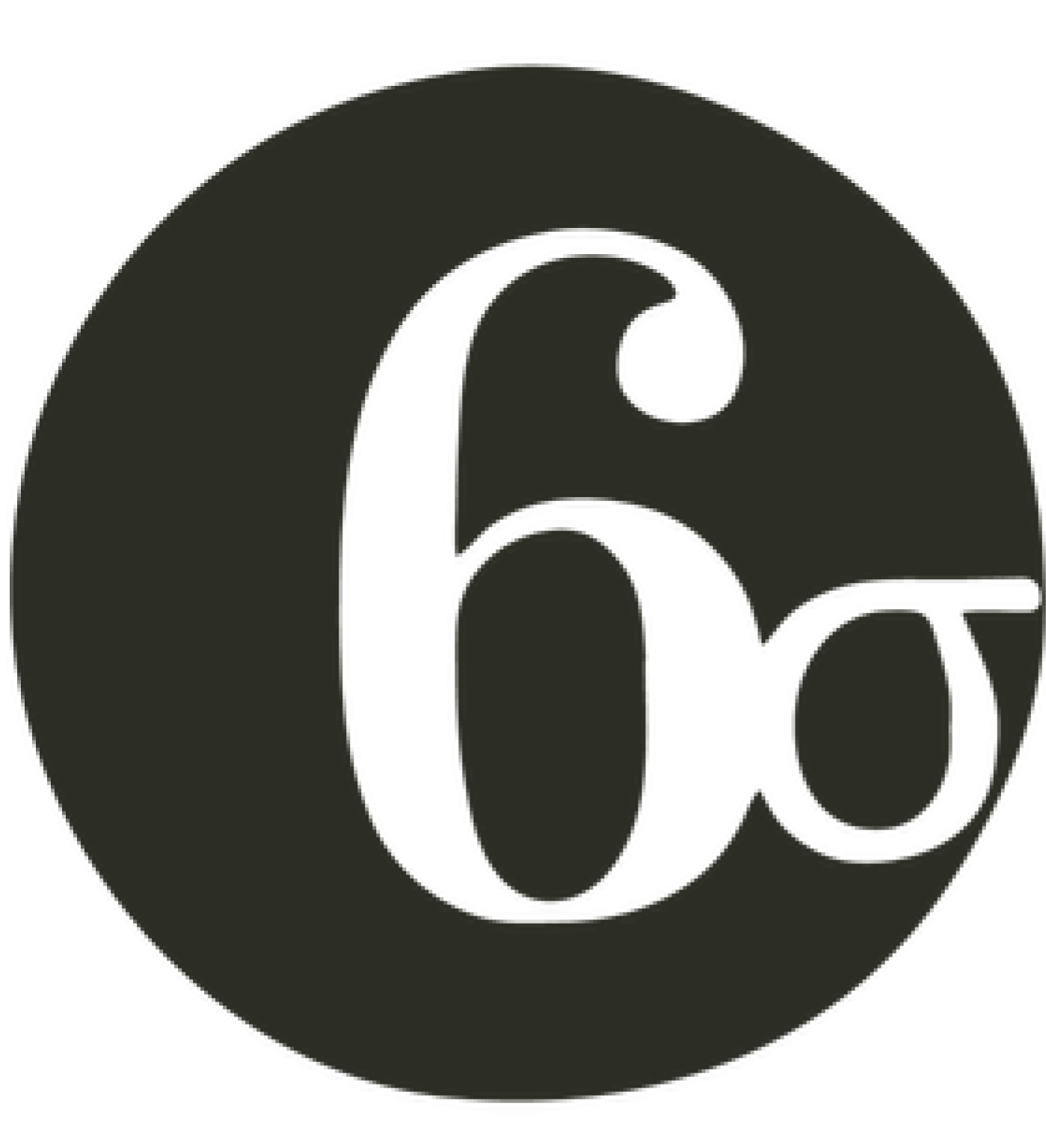
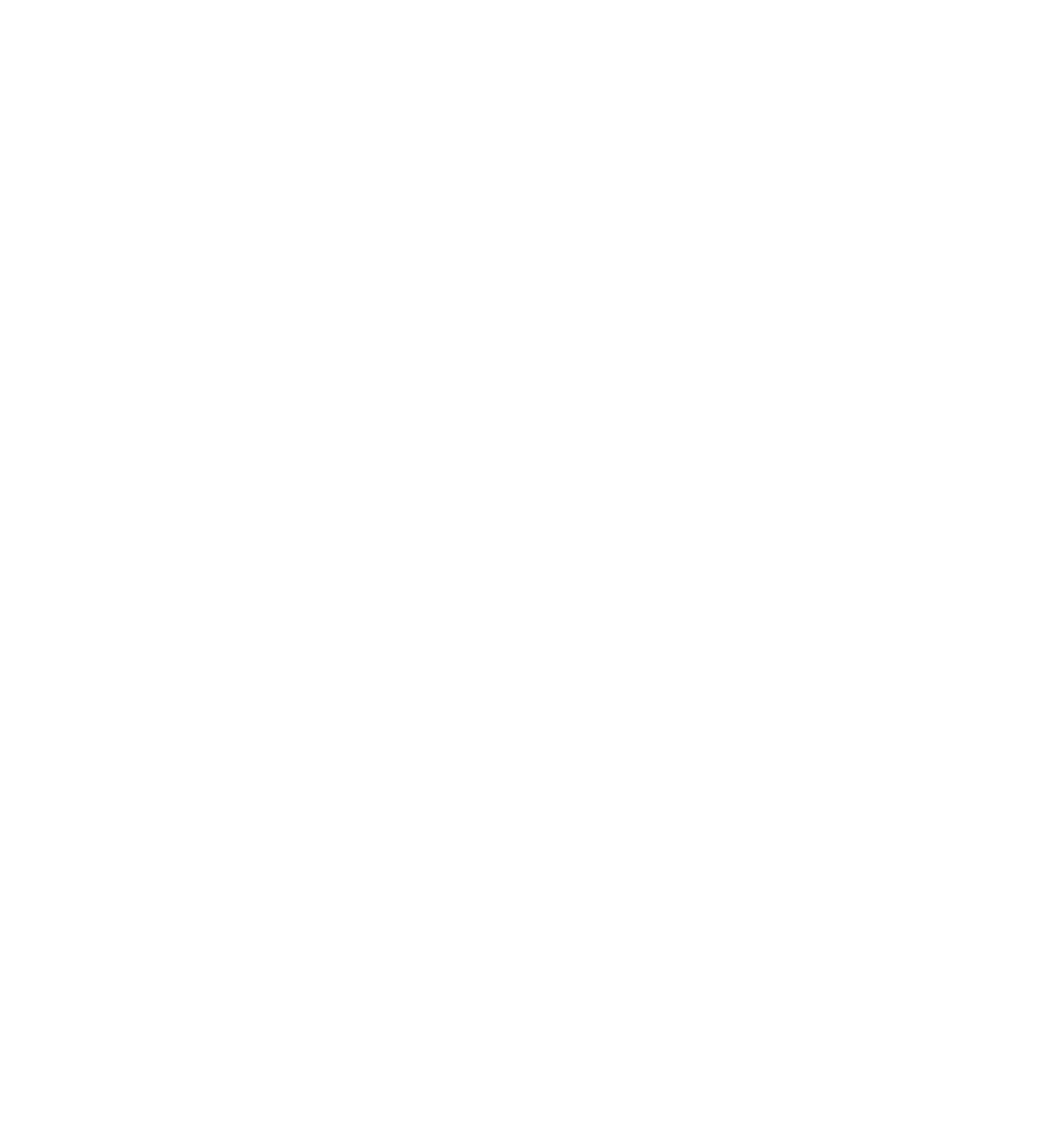
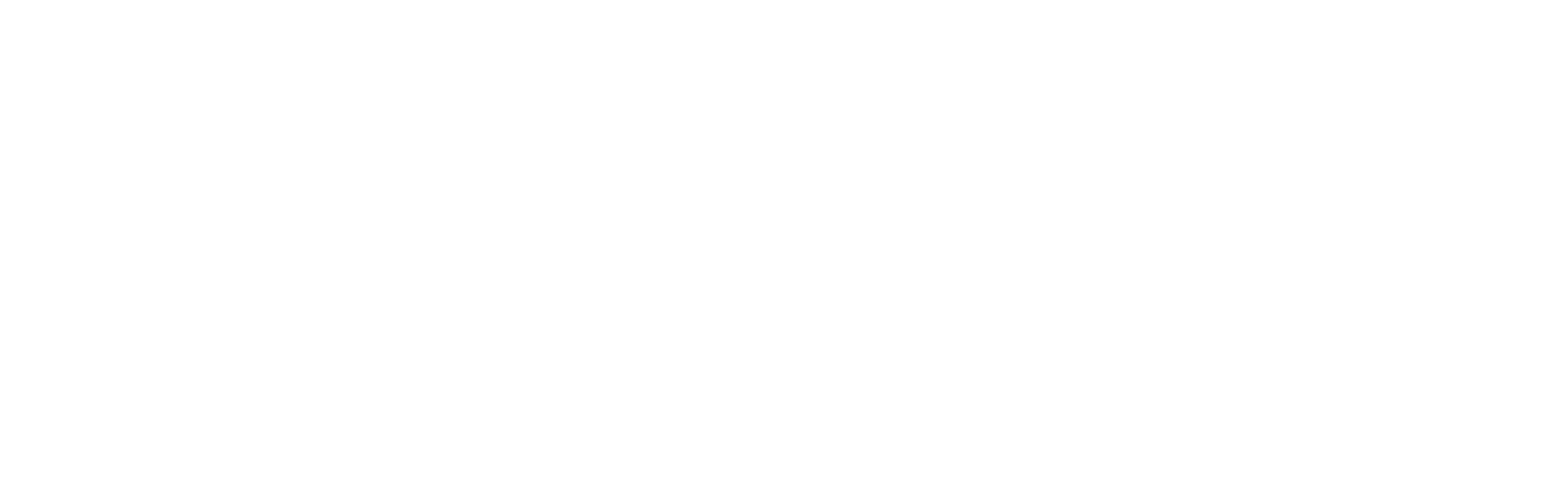
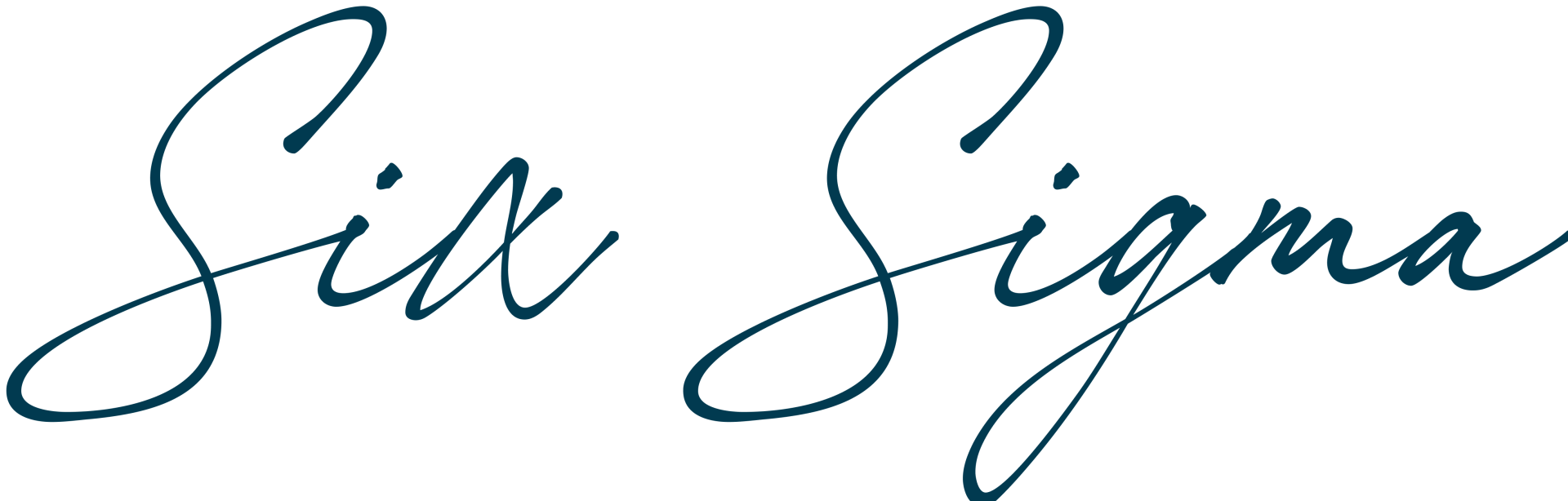
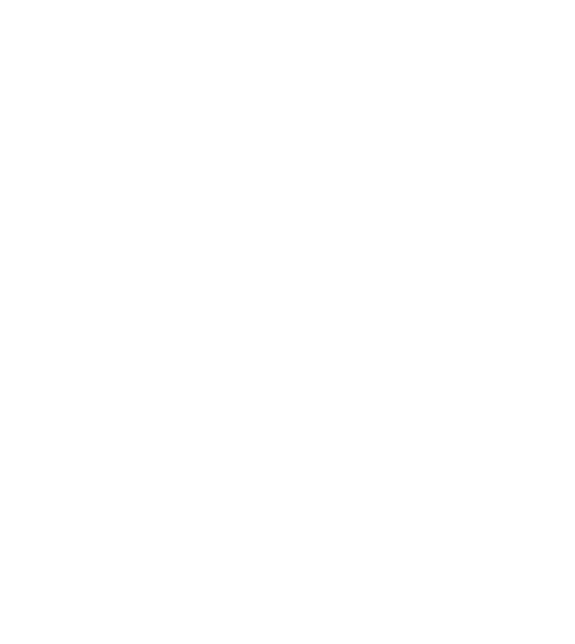
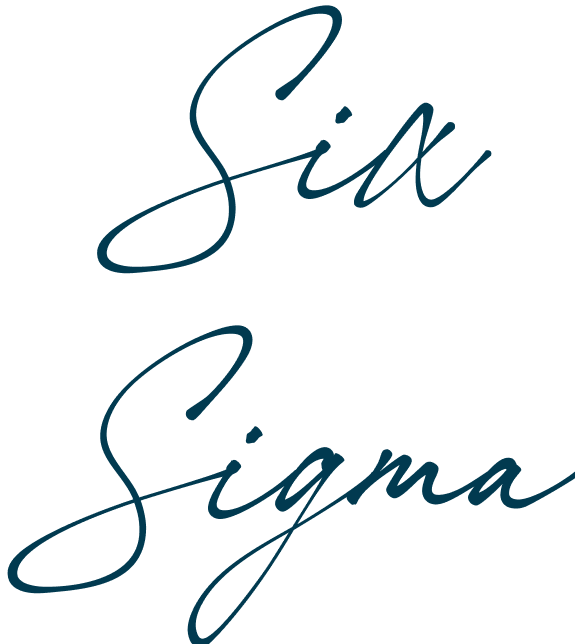
Focuses on quality and consistency, through process improvement and variation reduction.
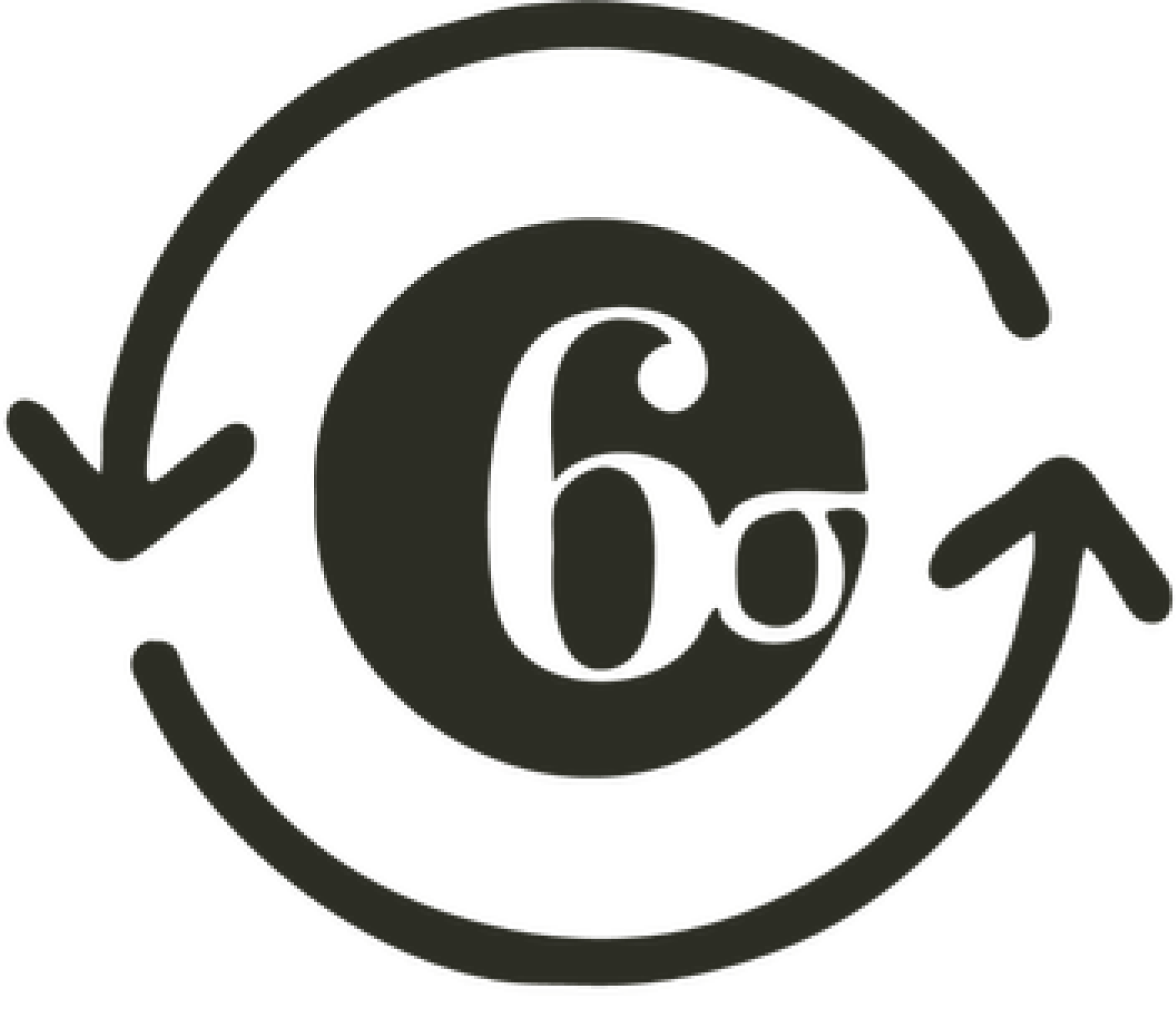
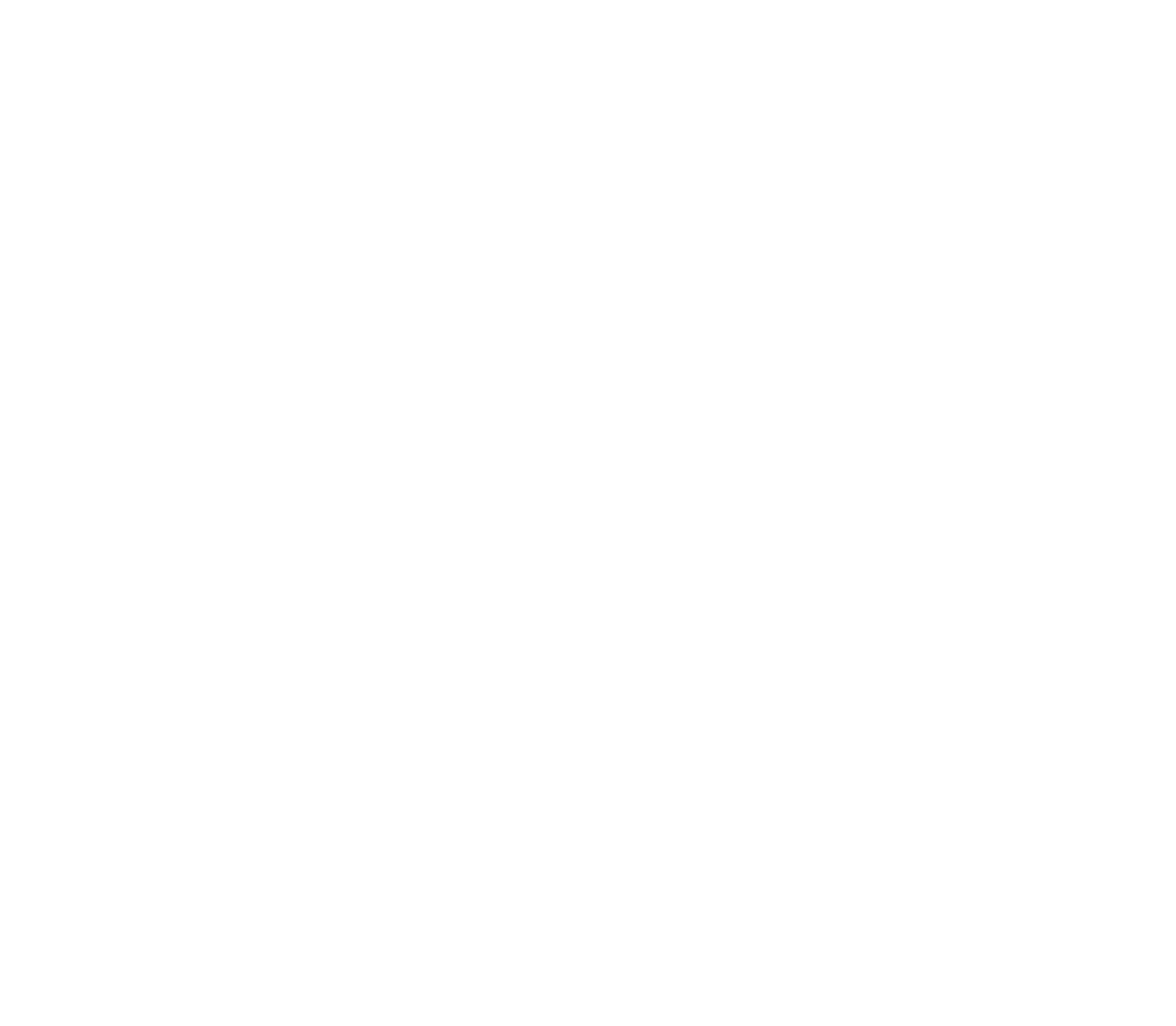
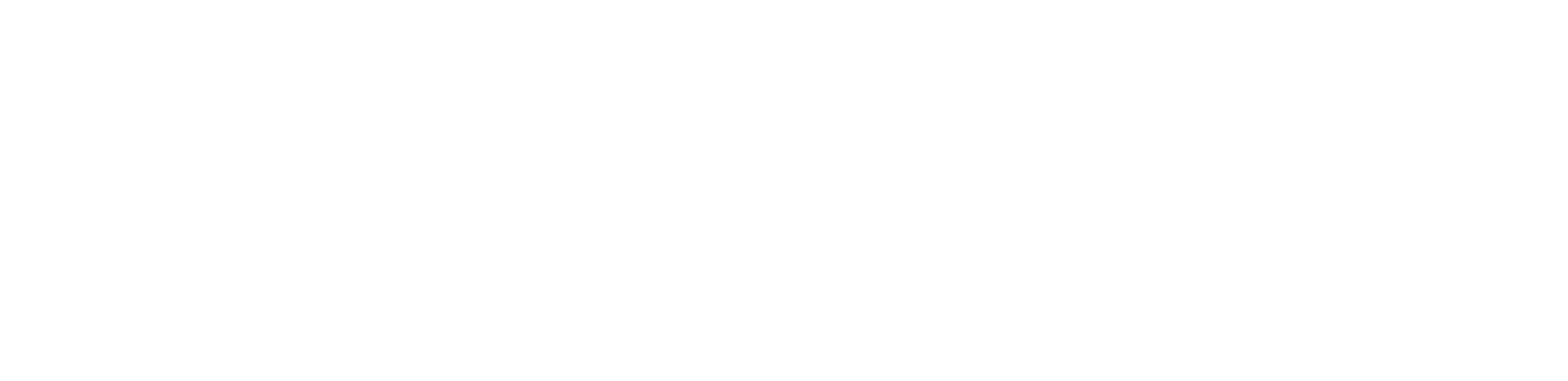
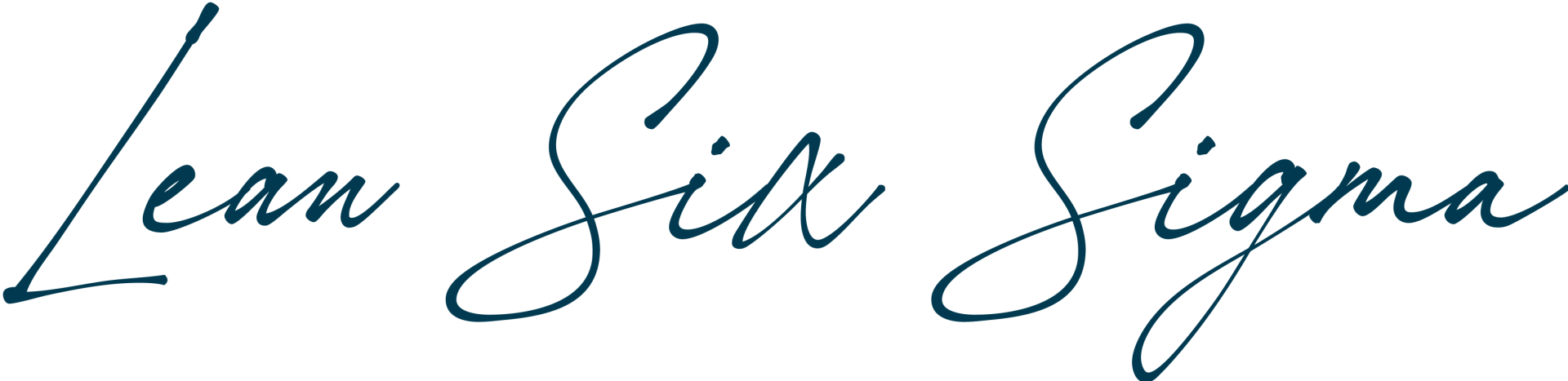
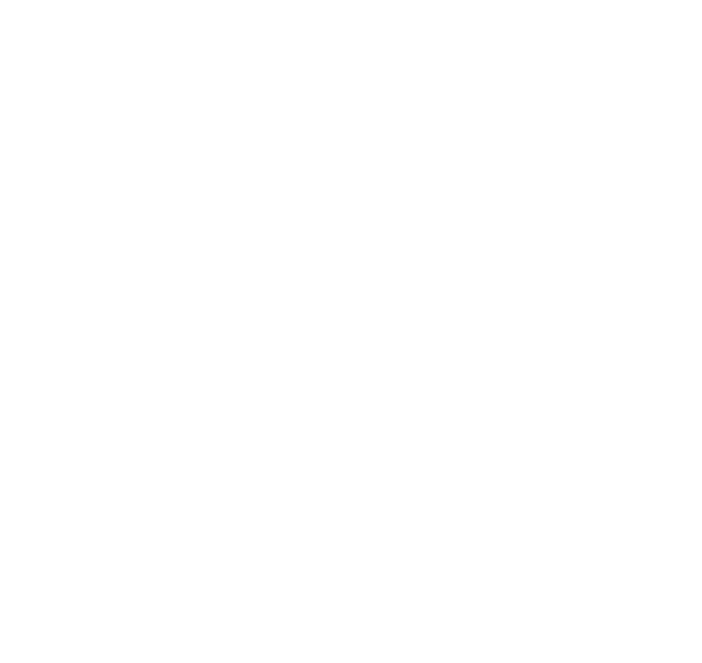
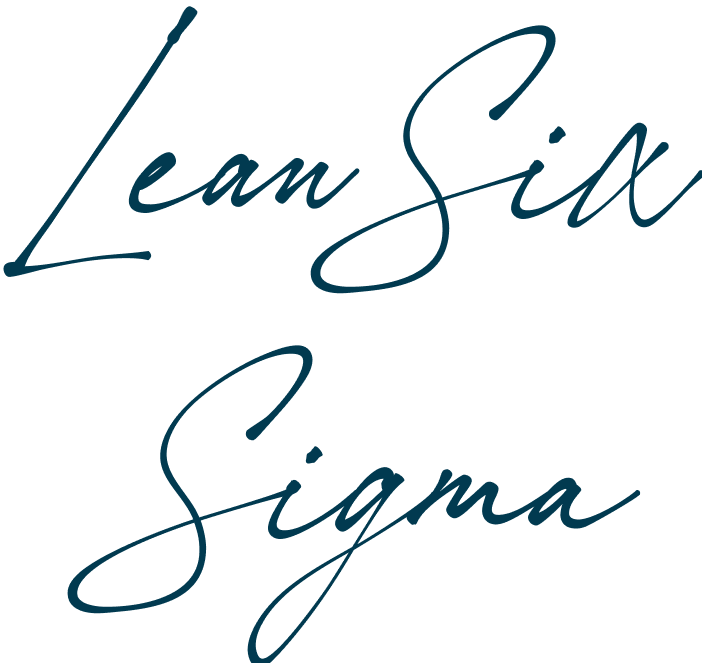
Delivers customer value through efficient operations and quality standards.
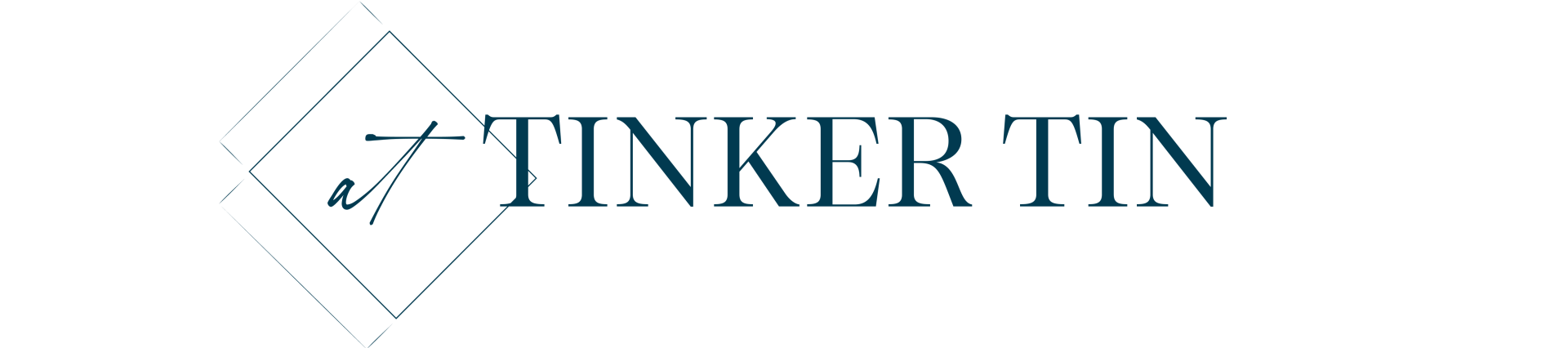
We combine Lean, Six Sigma, and Kaizen principles to create a robust customer-centric methodology driving both short-term efficiency gains and long-term process optimization.
Continuous Improvement has become ingrained in our organizations culture, leading to our sustained success.
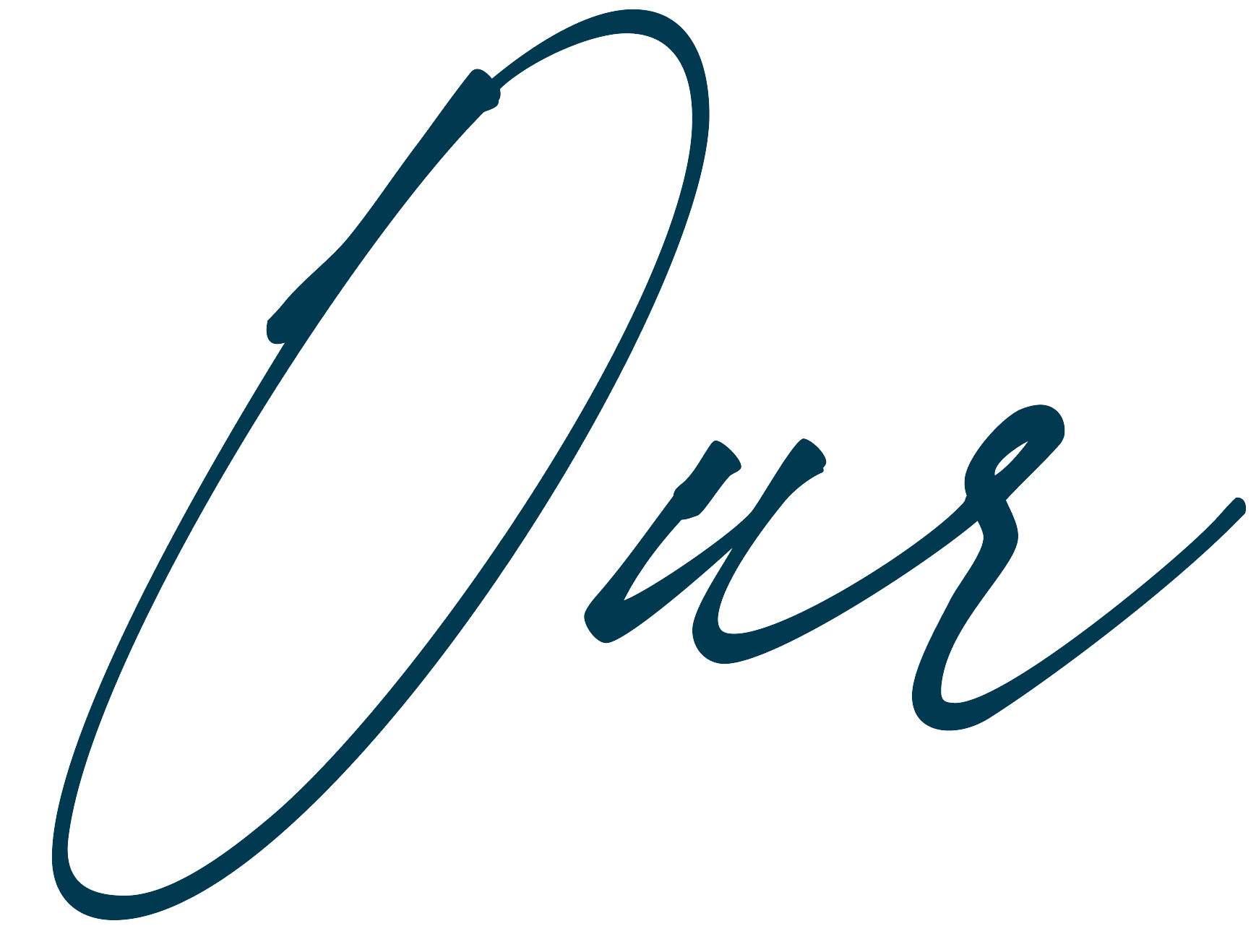
Methodology
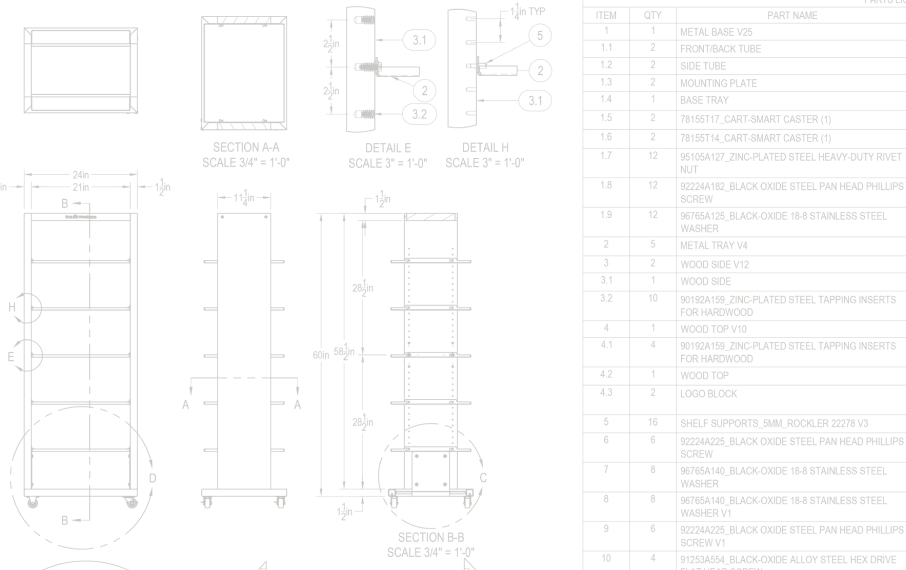
VOC (VOICE OF THE CUSTOMER):
A process to capture customer needs, expectations, and feedback to inform design and manufacturing decisions.
TEI (TOTAL EMPLOYEE INVOLVEMENT):
A practice that engages all employees in continuous improvement and problem-solving to enhance efficiency and productivity.
DMAIC METHODOLOGY:
A data-driven process improvement cycle (Define, Measure, Analyze, Improve, Control) used in Six Sigma to optimize processes.
SPC (STATISTICAL PROCESS CONROL):
A method of using statistical tools to monitor and control manufacturing processes to ensure quality and consistency.
VA/VE (VALUE ANALYSIS/VALUE ENGINEERING):
Techniques to improve product value by enhancing functionality or reducing costs without compromising quality.
VSM (VALUE STREAM MAPPING):
A visual tool to analyze and improve the flow of materials and information throughout the production process.
RCA (ROOT CAUSE ANALYSIS):
A problem-solving approach to identify and address the underlying causes of issues.
5 WHY:
A technique to drill down to the root cause of a problem by repeatedly asking “why” until the core issue is uncovered.
7S
A workplace organization method (Sort, Set in Order, Shine, Standardize, Sustain, Safety, Spirit) to create a clean, safe, and efficient work environment.
VOC (VOICE OF THE CUSTOMER):
A process to capture customer needs, expectations, and feedback to inform design and manufacturing decisions.
TEI (TOTAL EMPLOYEE INVOLVEMENT):
A practice that engages all employees in continuous improvement and problem-solving to enhance efficiency and productivity.
DMAIC METHODOLOGY:
A data-driven process improvement cycle (Define, Measure, Analyze, Improve, Control) used in Six Sigma to optimize processes.
SPC (STATISTICAL PROCESS CONROL):
A method of using statistical tools to monitor and control manufacturing processes to ensure quality and consistency.
VA/VE (VALUE ANALYSIS/VALUE ENGINEERING):
Techniques to improve product value by enhancing functionality or reducing costs without compromising quality.
VSM (VALUE STREAM MAPPING):
A visual tool to analyze and improve the flow of materials and information throughout the production process.
RCA (ROOT CAUSE ANALYSIS):
A problem-solving approach to identify and address the underlying causes of issues.
5 WHY:
A technique to drill down to the root cause of a problem by repeatedly asking “why” until the core issue is uncovered.
5 WHY:
A workplace organization method (Sort, Set in Order, Shine, Standardize, Sustain, Safety, Spirit) to create a clean, safe, and efficient work environment.